Holistic Test Strategies to Empower Your Product Lifecycle
We’ve all been there, it’s the last prototype run, and we didn’t take the time to fully understand how the product would be tested in manufacturing. Reactive test strategies are painful and typically only address short-term needs.
But what if a test strategy could be proactive, minimize the anxiety of releasing the product to manufacturing, and even accelerate time-to-market in the process?
Defining the Holistic Test Strategy
While typical test strategies focus primarily on production manufacturing and implementation, SMT Holistic Test Strategy encompasses the entire product lifecycle, beginning as early as possible in the design phase and revisited at key development milestones.
Although test coverage is a primary focus, the “when” and “why” behind the test integration carry significant implications for the Design for Test (DFT) process. By understanding the product’s end-use application throughout its lifecycle, engineers can identify various hooks and configurations needed, making everyone’s job just a little bit easier.
Aligning HTS with Product Lifecycle
To understand how product attributes impact the Test Strategy, it’s often helpful to work backward through the product lifecycle. Consider the following questions:
- What does the product roadmap indicate about the product’s active lifespan?
- What is the anticipated support plan after the product becomes obsolete?
- Will any testing occur in the field during the product’s operational life?
- If the product is installed in the field, is there a process for verifying successful installation?
- Does the product include subassemblies that may be field-replaceable?
- Can end customers or service teams return individual boards or subassemblies for repair?
- Are any boards conformal-coated or potted?
- Are any boards smaller than 8 inches square (or below a 4-inch width minimum for conveyors)?
- Will the product require configuration via hardware or firmware/software?
- If the product is processor-based, what level of diagnostic resolution is built into the firmware/software?
Key Technologies and Methodologies
Understanding the product’s attributes allows you to align test coverage with real-world requirements. By optimizing test coverage using available test and inspection techniques, you can eliminate unnecessary duplication and reduce costs.
The primary goal is to confirm that the electronic product has been built correctly at various manufacturing process steps. For instance, at the board level, test and inspection techniques should identify the following types of defects:
Each process step introduces a potential failure point, your test coverage must reflect that.
An effective test strategy also incorporates the right test hooks for programming, configuration, subassembly and variance, post-coating or potting checks, and pre-shipment testing at the required SKU level.
Test coverage is often dictated by test access. If you can access a group of nets, various techniques are available to test the electrical components on those nets. This is the foundation of In-Circuit Testing (ICT), which primarily focuses on component-level testing.
At the Functional Test (FT) or JTAG level, test access is still critical, but the focus shifts to verifying functional circuit blocks in a simulated end-use scenario. Firmware or software, once programmed into the product, can enable diagnostics by exercising specific functions such as memory access or data bus communication.
Benefits of a Holistic Test Strategy
A proactive test strategy that considers the product’s needs across its entire lifecycle offers several advantages:
- Enables the most cost-effective integration of testability during design
- Reduces reactive design respins to add test access or hooks
- Provides early input for generating test specifications during NPI
- Fosters proactive collaboration among design, test, and manufacturing teams
- Minimizes product returns through optimized test coverage
Conclusion
At SMT, our Holistic Test Strategy is embedded within our DFX services, specifically through DFT (Design for Testability). Together with DFM (Design for Manufacturability) and DFP (Design for Procurement), we help customers accelerate New Product Development (NPD) and New Product Introduction (NPI) timelines.
Let SMT be an extension of your team. We’ll integrate our DFX expertise into your NPD/NPI process to fast-track your product development and empower your product lifecycle.
Join Our Subscribers!
You May Also Like
These Related Stories
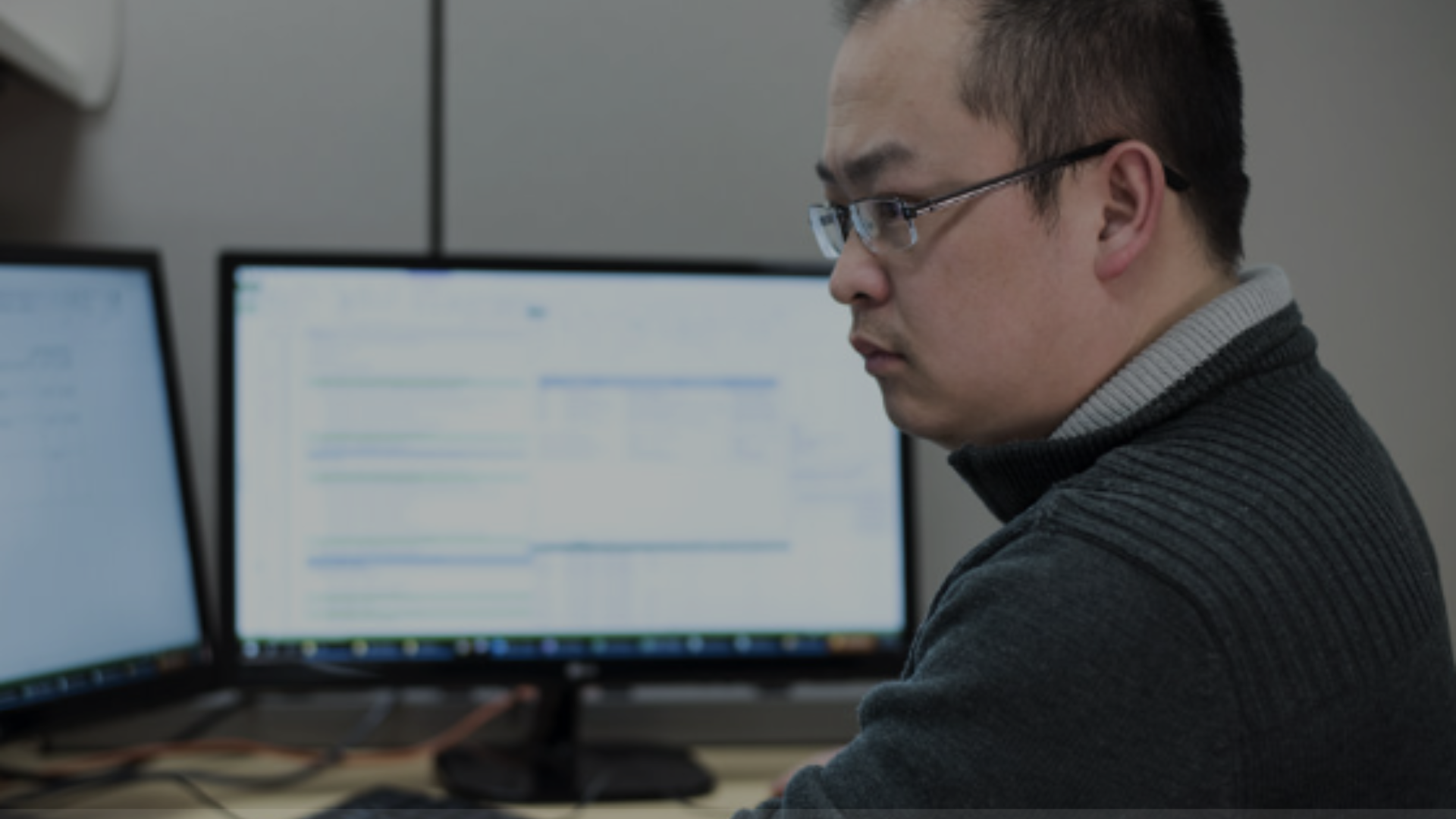
Project Management - Planning for Risk
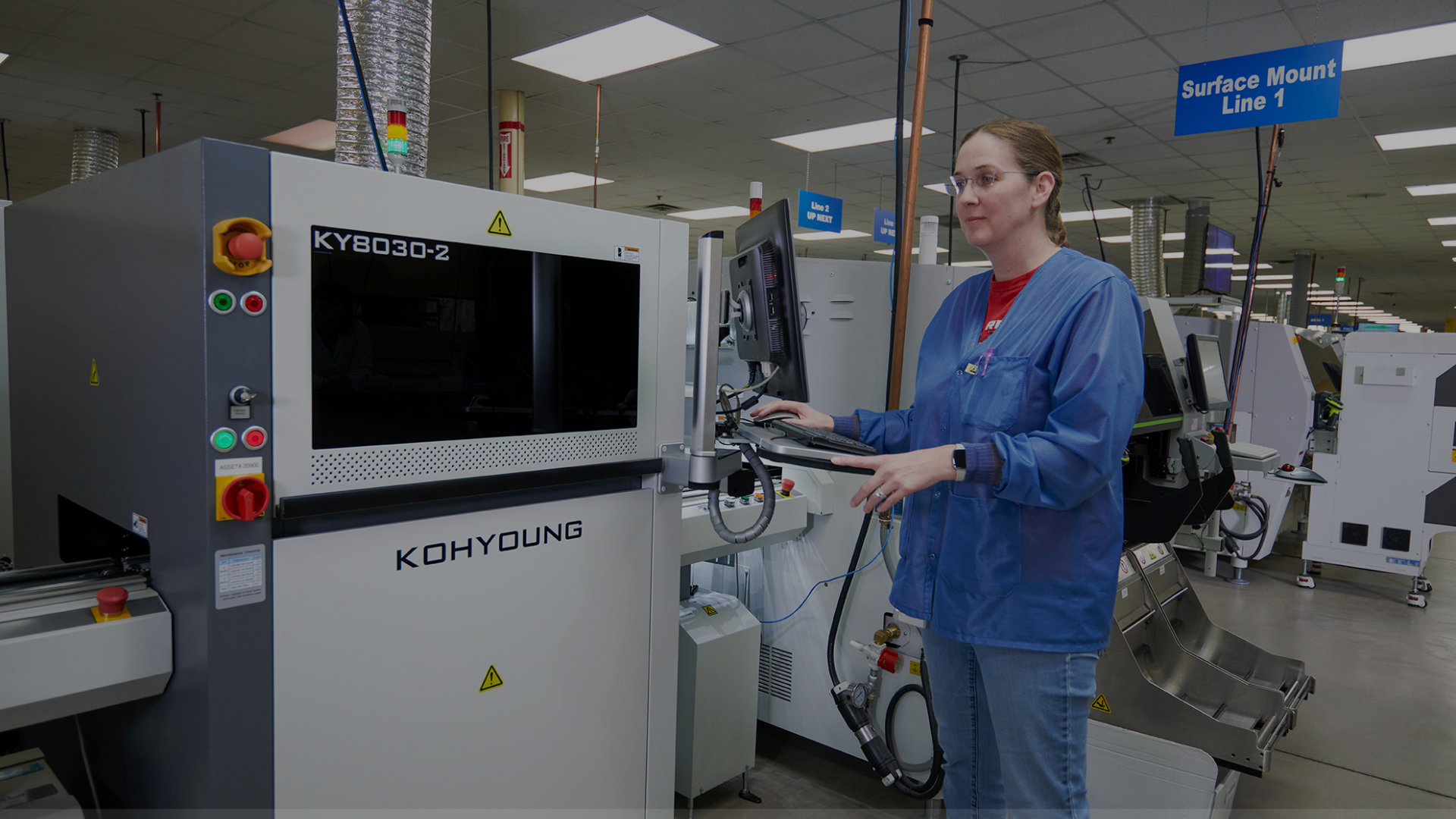
Everything Under One Roof - Design to Manufacturing
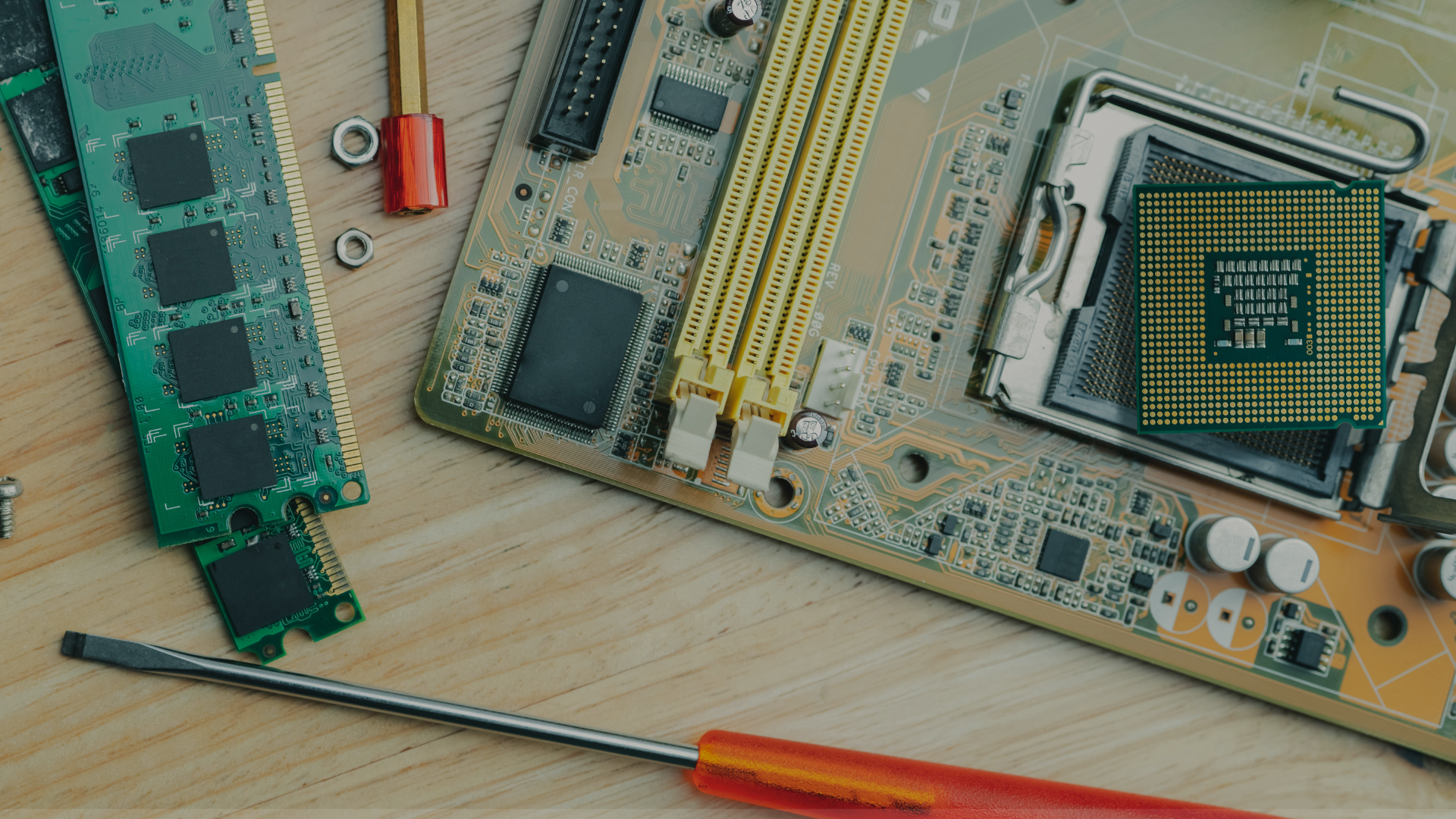